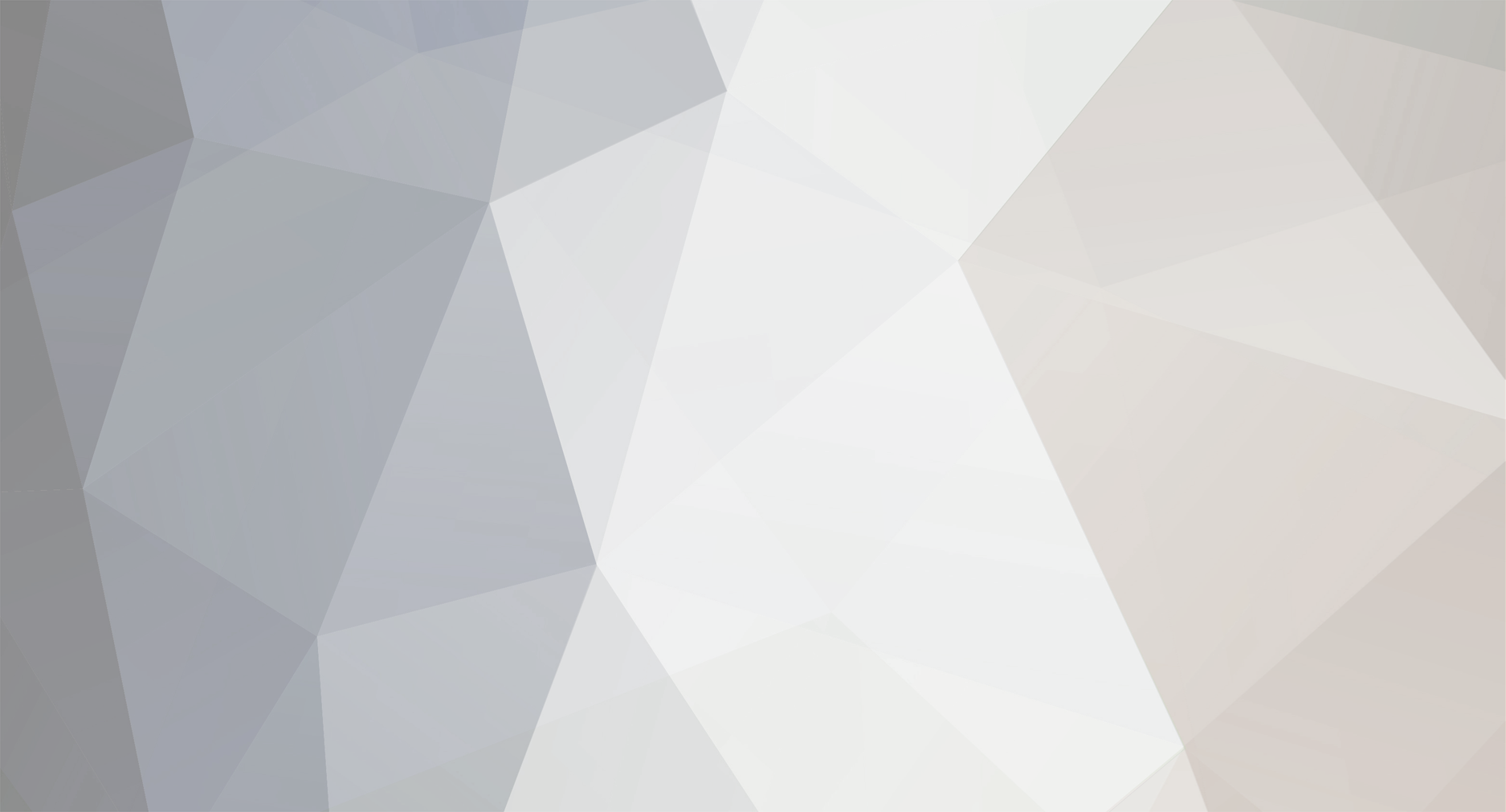
Tinman
Members-
Posts
1,399 -
Joined
-
Last visited
Content Type
Profiles
Forums
Gallery
Store
Events
Everything posted by Tinman
-
Decklid is done. And it took quite a bit to get it to fit. First I had to correct the unevenness in the rear quarter panels. I busted out my trusty cutoff wheel and made a slice in the driver side. Widened the slice to a full 1/4" where it turns 90 degrees, pulled it together and welded it up. Sorry, only picture taken of this was the tack weld stage. Then I ground down the leading and side edges on the decklid to remove where it folds over the under bracing. Tossed the heavy under bracing and made a lip that the decklid skin would weld to after it was trimmed to size. The lip is made from 16ga. cold rolled steel strips that were clamped to the truck opening with 1/8" shims, scribed to the top of the opening, and cut to match. In the forward corners it was only 1/4" tall and very flimsy so gussets were added. The decklid was then laid on top and marked for it's trimming. 5/16" off of the leading edge, 1/4" off of the driver side at the rear, nothing at the driver side front, and 1/8" off of the passenger side. This left a nice corner to corner joint to allowed it to be welded to the lip cold with tacks only yet still get full penetration. After welding complete and welds ground down. And finally installed four of these little guys. Quik Latch mini fasteners in the 1" O.D. size. They are finicky to get to release properly but when dialed in they work great. I'm in the process of fitting springs under each one to help the decklid release from them easier. As it is now, as soon as I release the forth one, one of the others snaps back on.
-
Thanks everyone! Here's a quick video update. Still suffering growing pains in this whole video making and editing. Welding is so much easier. Not much else to see in this video. Hope to have more and better video in the future.
-
The "Explorer tread lightly" would have been a much better name to forget 5 years from now.
-
So, it's been a little more than two weeks, maybe closer to two months, but I still think with only just two more weeks this project will be complete So, making videos is far more difficult and time consuming than I expected but I have not given up hope. Well, I have, but not all hope. There is still a glimmer of hope that I intended to nurture into something worthy of wasting your precious time with but it might be another "two weeks" For now, some photos. The first slice. I cut the rear quarter panels at peak of the valley? How can there be a "peak" in a valley? What's the opposite of "peak"? Whatever that is is where I made the cuts. I figured this would be the best place to add a filler strip to widen the body at the beltline. This way filler would be minimal. The original intention was to widen the body 3" on each side and add fender flares to cover the tires from there. After cutting and sliding the rear quarter panels out the intended 3" I realized it would not work. By adding a consistent 3" in width, there would be another 3" of flare required in the front and nearly nothing in the rear. This would not work. So, after a few beers, some measuring, and a few minutes... or hours of staring at it, I formulated a modified plan. The body would be widened but at different increments. 3" at the front, 2" where the doors meet the fenders, 1" where the doors meet the quarter panels, and lastly, 1 1/2" at the rear. I felt it would look best to keep the inner tail lights at their factory Ford location, move the outer tail lights with the quarter panels, and move the center tail lights halfway, 3/4". The Howe chassis is a 104" wheelbase, the 1968 Mustang is 108" wheelbase. I've found a few places to narrow the gap between the two. One is at the rear quarter to roof panel meeting point. I was able to gain 3/4" here but doing so caused a misalignment in the drip rail. After some trimming, welding in a filler strip and additional filler metal, and some grinding, it's ready for filler... or so I thought, every time I look at it, I find more places that need some fine tuning in hopes that a high build primer might be all that's needed.
-
LOL! Ah, that's so relevant that it hurts, like a kick in the nuts hurts.
-
I'm sorry the updates are not more frequent. And even more so that the finished product is way off in the future. Went on vacation, now catching up from vacation. More progress will be made and documented soon.
-
Two weeks.
-
Thanks everyone! I did not notice the lack of volume when editing, only after viewing it on youtube. I was using an external microphone but I'm guessing I was just too far away from it, or I just need to speak up. I'll be sure to come up with a solution for the rest of the videos. Locating the body on the chassis was all done with the original coupe shell. Once it landed where it fit, I took multiple dimensions and pictures, even pictures of an angle finder laying on different areas of the body. Most of the dimensions were to the windshield frame and cowl. Then everything was stripped off and the windshield frame and cowl were set back in place according to the dimensions taken and the new sheet metal was fit up from them. The only issue I almost ran into was the roof skin to main roll hoop. The fastback roof slopes down towards the rear much more so the the coupe's roof, but there is still roughly 1/4" gap at the tightest point where as the coupe's roof had over an inch of clearance.
-
Please excuse my shortcomings both in front of and behind the camera. This is just an introduction video, hope it doesn't put everyone to sleep.
-
Thanks all. First video in progress. Production value will be very limited as it's quite the learning curve for a non tech savvy guy like myself.
-
Very extensive trial and error. This is one area the beer consumption really helps. Step back to take a drink and damn, see that it's not quite right yet.
-
Okay, full steam ahead on this project now... after vacation next week. I'm nearly finished fabricating the mounting points from the beltline up. Once they are complete, it's time to cut the skin up and make it 6" wider. In order to both document this project a little better and keep me more motivated, I'm going to start a build series on youtube. If all goes well, next update will be in video form.
-
Okay, it took way too long to get back on this project but the new mufflers are finally done and..... I don't know if I like them. The new mufflers are a bullet style. Straight through perforated core wrapped in 1/4" of fine stainless steel wool and then an inch of a ceramic wool insulation. 2 1/2" I.D., 5" O.D., and 9" long. After getting them done, I bolted them on behind the X pipe that did not work well in my opinion with the factory mufflers. I was bound and determined to use the X pipe and I hoped it and the new style mufflers would make the proper music. Once again, I was wrong. The nasty trumpety noise was back at 2000rpm. It's a very odd phenomenon, it goes as soon as it comes. Lasts for only a narrow rpm range, maybe 50rpms and only while accelerating. I could not get it to make the same noise at any steady state rpm. But every time I passed 2000rpms while going through the gears it barked at me like an annoying jack russel terrier that wanted attention and badly. So the X pipe is no more. I cut it out of the exhaust mid section and set it on the bench thinking I could use it elsewhere on another project. The mid section was welded back together sans X, reinstalled, and ready to make better noises. The more I drive it, the more I'm growing to like it. Not sure if I'm getting used to it or if the packing is breaking down a little. I recorded a three gear pull to hear it from outside the car and I'm still undecided. I'll give it some time but at this point I'm thinking the "bypass mod" on the factory ti mufflers might be the way to go. Anyways, here's how it sounds as of now.
-
Yep, my annual post. See y'all next year... No apologies necessary. I'm sure they would both have laughed at your comment.
-
Give my former teammates some slack. Sam and Travis are excellent writers and drivers. Both skills that far outweigh youtube presence. I wish they were not reading from a script because when these two are shooting from the hip in a casual conversation, it is beyond hilarious.
-
I rearranged the garage a little while back. Workbench is now on the back wall and the toolbox is in front of the lift. Thanks!
-
I've been slacking big time on this project and to put it even further behind, I've started to make some new mufflers for the Z06. Once they are done I plan to make some more progress on the Mustang. As of now it sits like this, Front clip is mounted and the windshield frame/cowl panel are tacked to the roof.
-
Nice score. Bring it to the track with corners! I have a set of C5 Z06 wheels in black I would let go for cheap.
-
I'm sure there are plenty of automotive specific tapes for such an installation but this stuff, https://www.mcmaster.com/75935a21 has really impressed me. We have used it to bond stainless panels together. The panels will bend before the tape releases. It's available in different widths and thicknesses too, just search for double sided tape on McMaster Carr and click the VHB option.
-
I do enjoy my job and even better, I get to make love at my job. Fabricated this from 1/8" stainless steel and a coworker and I polished it to a mirror finish. It is being donated to the Make A Wish Foundation for their auction.
-
Some minor progress, much less than I was hoping for. Aftermarket body panels and I just don't get along. I like to measure in thousandths of an inch while the producers of these panels seem to like to measure in kilometers as seen from a satellite miles above earth's surface. Working for just a few minutes to get the panels true, straight, and square ends up in frustration, beer drinking, and blank stares. Next thing I know, it's a month later and I'm no where near where I would like to be. So, as of now, here is where the project stands. Rear quarters, tail panel, and roof panel mounted to the chassis. Removable front clip taking shape.
-
It might be best to find a builder that can jump through all the zoning ropes for you. Also, deeper is better than wider in my opinion. If you have to go rectangle, put the door on the short end. And make it tall enough for a lift if at all possible.
-
I have no recommendations. I'm just here to show support for your wise decision. In the case of garages, bigger is always better.
-
I'll have to describe the widening process in pictures when I get to that point. But for now, think of or google image search "IMSA GTO". The greenhouse will remain as is but the fenders and doors will be pushed out and fender flares made. I need around 6 1/2" per side. I'm currently debating how much will come from the sides of the body being pushed out and how much will come from the flares. I hope to have the quarters and roof mounted to the chassis over this long weekend. Next step will be a removable front end, after that, the widening process can begin.