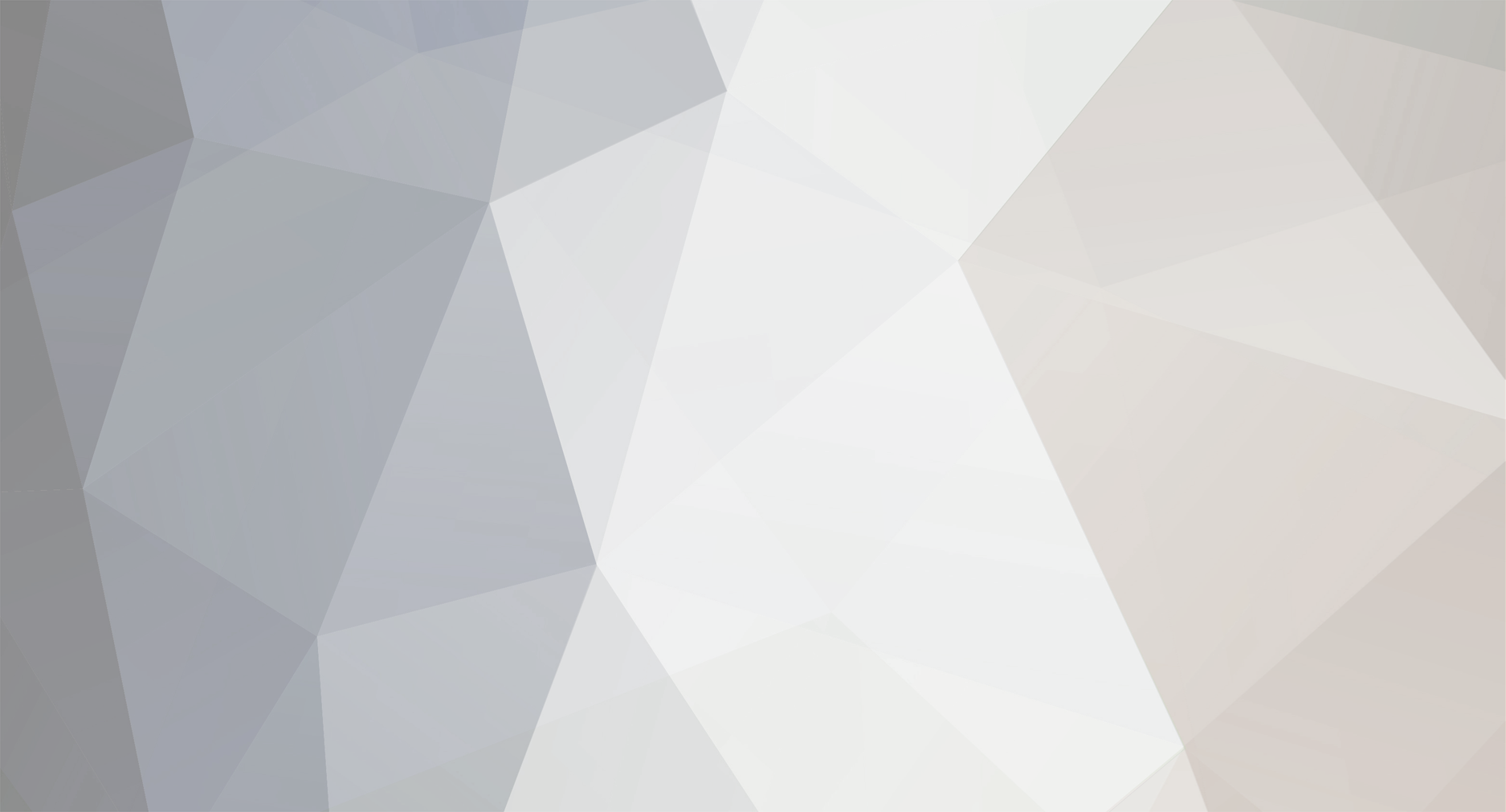
Tinman
Members-
Posts
1,399 -
Joined
-
Last visited
Content Type
Profiles
Forums
Gallery
Store
Events
Everything posted by Tinman
-
So the Imovie app has a cool little trailer template. Updates will be coming.
-
I have some Z06 springs and shocks with around 67,000 miles on them if you are looking to improve handling a tad.
-
The patina is perfect!
-
Excellent!
-
Try one, you'll never go back to hard wheels. Thanks for the hookup!
-
1975 Rockwood Roadking 2002 - the new "family truckster"
Tinman replied to zeitgeist57's topic in Passing Lane
She's a beaut Clark. -
1975 Rockwood Roadking 2002 - the new "family truckster"
Tinman replied to zeitgeist57's topic in Passing Lane
You can't type "Dodge" and "1975" without including pictures! -
Nice. Thanks. It will be interesting to see what that goes for.
-
Lol. Thanks. Cold snacks, aka, beer is currently supplying adequate moral support. Where are you currently located?
-
Relocated the ignition system to work with the hood vents. It was mounted to the same X brace but horizontally. By flipping it vertically, it gives the yet to be made ducts more room and will allow them to go nearly to the bottom of the radiator. Just some simple pieces of 1/2" square tubing welded to the 1" round tube of the Howe X brace.
-
Contact Turborust. Derik has owned at least one of these.
-
Nice. Is that massive grill a single piece or is each bar separate?
-
Much thanks gents. It was time to revisit the rear bumper to make it flow better with the body lines. I had already done some of this when I widened it. I added 2 3/8" to the width of the bumper whereas the rear of the car is 3" wider. This helped a lot but it still needed to be made taller to come closer to the rear fender extensions. And the rear fender extensions needed a little trim. I started with a couple of pieces of 14ga. formed to the profile of the bumper. Added a V shaped cap and started on the welding and grinding. More welding, fitting, and grinding to get it close enough for a skim coat of filler. The fender extensions will need filler as well as they did not take to welding very well at all.
-
Much thanks good sir.
-
Noted. Should be much easier in this case as the centerline of the engine is roughly where the hood meets the cowl.
-
Thanks. If the air were to hit the radiator and deflect off of it, yes it would have a lifting effect. But if the air goes through the radiator and out of the hood, it should have the opposite effect. I plan on fully ducting every bit of air entering the grill. Some to the brake rotors but most to the radiator and from the radiator, full ducts to the hood vents. I did something similar to my RX7 and the results were very noticeable, even to the point my co drivers felt the car was balanced too favorably to the front.
-
Had to revisit the radiator mounting as the Mustang body lent itself to the opportunity for some increased cooling capacity and more importantly, front aero downforce. The 1968 and 1967 Mustang GTs came with front turn signal indicators on/in the hood. I'm not sure if it was GT specific or an option, die hard Ford fans please chime in. I decided to mimic the body lines of the turn signal indicators but have the recessed areas dive much lower to evacuate the air that passes through the radiator upward through the hood instead of going through the engine bay and then under the car. This should help with both cooling and create some front end downforce or maybe better put, reduce front end lift. In order to make this possible, I had to remount the radiator. Slightly higher and with a forward instead of backward lean. New lower mounts were made from 14ga. cold rolled steel and welded to the frame and the upper mounts relocated and connected to new tabs welded to the radiator with high temp rubber isolators. Then it was time to slice some sheet metal. The flat, non GT hood that came with the shell turned out to be an issue as it seemed to have been stripped of it's e-coat, left to rust, and then covered with some crappy black paint of some sort. Instead of pitching it, I'm using it as prototype material for the heat extracting vents. Yet another detail that will require more time and expense but I feel will be well worth the effort in the end.
-
Much thanks. I do want to keep the original lines as close as possible with two major exceptions, the wider overall body from the beltline down and the fender flares. The A pillars will stay where they are in a similar fashion to the 80s and 90s IMSA GTO and GTU cars. But instead of the fenders covering the wheels I'm going with a half and half method. First half, widened body, second half, fender flares.
-
Lol. The automotive hobby needs a new word for "finished" as the projects never are by definition, finished. Some good progress on the bumper. It's been widened and main brackets are done. Still need secondary brackets where it wraps around the fenders but those will come after the fender flares are done. I cut two strips of 14ga. cold rolled steel the width needed for widening and a little longer than the stretchout of the bumper profile and broke them up in my bench vise with the handy little press brake jaws. Back and forth to the profile template until good. I didn't get any pictures of the main brackets, they are just simple angle iron with speed holes drilled in for a little weight savings. I also tuned up the body lines on the fender extensions a little to match the fenders better. And now that it is to this point, I'm probably going to change the fender extensions by moving the headlights outward which will mean scrapping these and starting over. But I'll do the fender flares and front spoiler first so I can look at the whole picture and go from there.
-
Thanks! Wow, nice movie reference. I've seen the film but didn't remember that exchange of dialogue.
-
Again, much thanks for all the kind words! They are very appreciated and motivational. I finished off the filler strips all the way to the front and added a flange to mate to the extended headlight surrounds. Now came the ugly part. The headlight surrounds are cast from pot metal, a mixture of different metals that are easily cast into complex shapes but due to all the alloys mixed in, not considered weldable. But I figured I could make it happen well enough to be structurally sound yet would need body filler to be pretty. Here's what a clean piece of 3003 aluminum welded to 50 year old cast pot metal looks like, Not at all pretty but it holds quite well. Then it was just a matter of tacking on little pieces at a time. Then welded them out and ground down the excess of the beads. I was planning on cutting in ducts like cruzin01 mentioned in the style of the 1970 mustangs. But there really isn't enough real estate to pull it off and look right in my opinion. For now, I'll let them be and when the fender flares and front spoiler are done I can get a better idea of what will look best.
-
Thanks again for all the kind words everyone. Started attacking the front fenders for widening. First step was to find the low point in the fenders and break out the cutting wheel. Then slide it out on the three temporary supports clamped to the chassis, mock up the door, and inspect the body lines. After lining everything up I decided on 1 3/4" wider at the rear of the fender and 2 1/2" at the front. I supported a piece of 18ga. cold rolled steel underneath, traced out the required filler piece, cut the filler piece out and welded it in. I only went so far in the front as of that time, I didn't know exactly what I was going to do between the headlight surrounds and the wider fender. Then i had to take it off the jack stands so I could look it over from a slight distance to make sure everything was jiving so far. Extended the lower valance to meet the wider fenders at the bottom. Filled in the side marker lights to at least the point of the yet to be fabbed fender flares and decided to fill in the cut outs in the valance for the outside bumper brackets as the bumper will be mounted differently.
-
Despite the cold weather sucking nearly all motivation from my soul, a few minor things have happened. The fender extensions needed extending to close the gap from them to the decklid. I formed some extension extenders from 1/8" 3003 aluminum and welded them up. Here is the tricky part. The fender extensions are cast from pot metal, not a material that can be welded. But it can somewhat be adhered to if it consists of a decent percentage of aluminum. I got lucky with these. Just a little washing of the tacks and bead towards the pot metal while concentrating the heat on the 3003 aluminum extension extenders. Finished result is not at all pretty but sound enough to hold together. I thought about leaving the keyhole for the trunk lock as a nice veiw point for a rear facing camera when on track but decided to go ahead and fill it. In this pic, you can also see where I widened the rear bumper. And the full view. I'm not sure if I'm going to paint it body color or try a chrome wrap on it. There will be some more welding on it to extend it upward closer to the fender extensions at a later date. Next up, the truck stop tail lights. Since the tail lights were widened, I needed to cut the lenses into three pieces and make new housings. The new housings are two piece and fabbed from .063" and .080" aluminum. One to hold the lenses and one to house the universal led tail lights, the same kind found on tractor trailers and such. Just a couple more minor items to address on the rear and then it's time to spin her around and start widening the front fenders.
-
Much thanks everyone. I like them but I do wish I had gone with the tried and true Dzus fasteners. The one thing that impressed me the most is the holding power they have, very tough little guys. I think they might be better suited for more flexible body panels as well. On steel, the alignment is finicky.