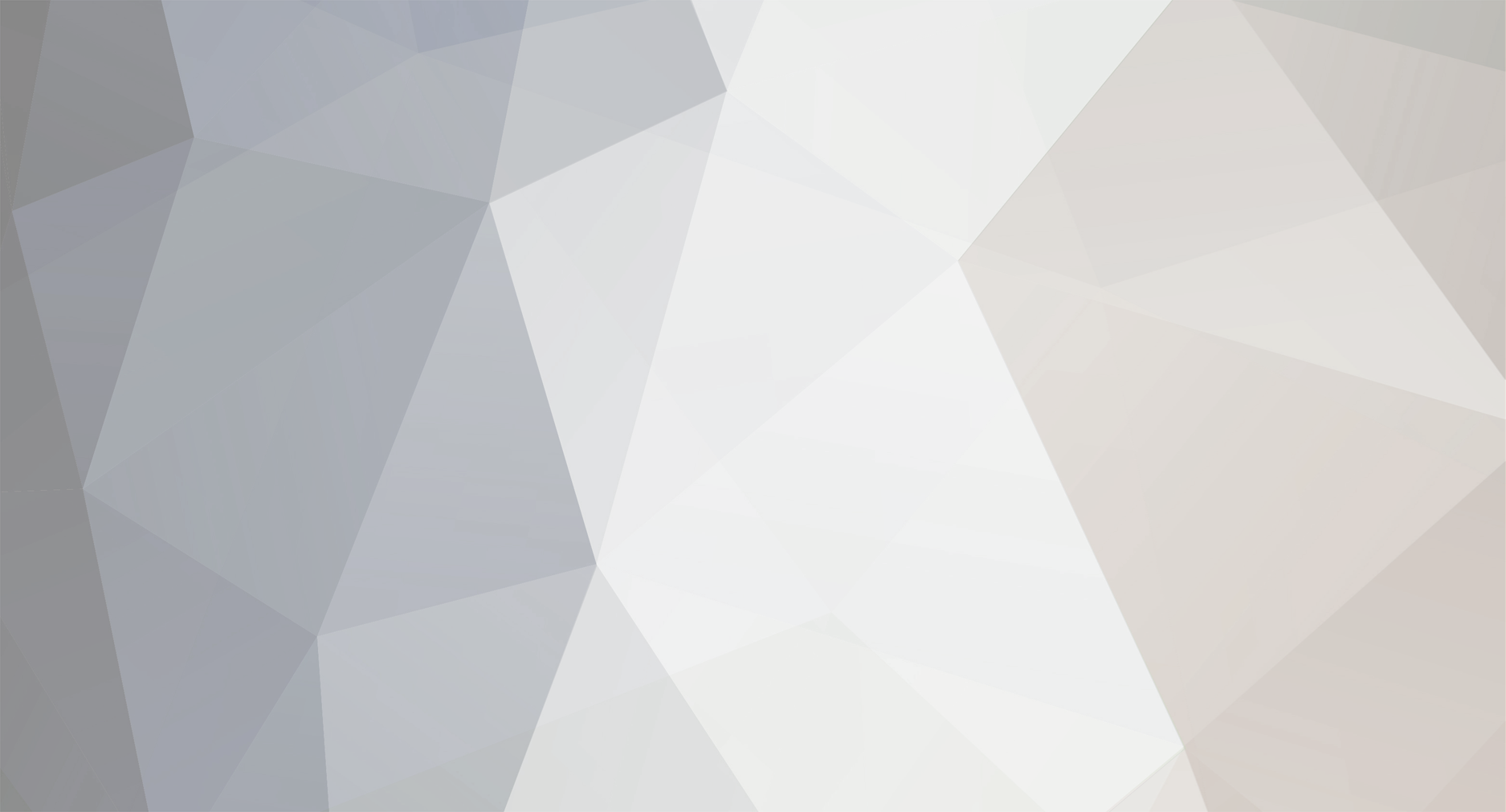
Tinman
Members-
Posts
1,399 -
Joined
-
Last visited
Content Type
Profiles
Forums
Gallery
Store
Events
Everything posted by Tinman
-
A little progress. Roof, quarter panels, deck filler panel, and tail light panel now welded together. Next step will be fabricating a removable mounting system to secure it to the chassis. After that, mount the cut off wheel to the angle grinder and cut into pieces. She needs to be wider, much wider.
-
Did they bring the Pontiac Aztec design team out of retirement?
-
New panels have been ordered. The rear quarters and roof skin have arrived, still waiting on the rear deck filler panel, decklid, and rear tail panel. The windshield frame and cowl panel have been trimmed down, media blasted, and treated with rust converter in the nastier areas. I welded in a patch where the rust had run a train on the lower driverside corner of the windsheild frame and filled some holes in the A pillars. The roof panel, windshield frame, and cowl panel roughly in place. Please excuse the pieces of deceased tree corpses used to get everything to the near proper elevation. I should be able to get the quarter panels in place soon but won't be able to lock them in place for the drastic modifications needed until the rear deck filler panel and decklid arrive.
-
Time to make some more progress Yeah, this looks a lot like a step or two back and not progress. The whole process to this point was to locate the windsheild frame and cowl to the chassis. That has been done and multiple measurements were recorded. Everything currently sitting on the chassis now is scrap metal. Here is all I'll be using from the original Mustang that was built by Ford in 1968 and even most of it will be scrap metal also soon. I cut away most of the lower cowl area but retained the upper windshield wiper motor bracket mounting points and the windshelid wiper arm pivot mounting points so I could retain the factory wiper motor and linkage. I will find a way to fasten the lower wiper motor bracket further down the road. Or, most likely, make a whole new motor mounting bracket with a different lower mounting point. With the loss of the lower cowl panel, the windsheild wiper pivot mounts became quite flexible so I welded in a couple of gussets. The driver side is as stiff if not more so than before but the passenger side is still a little more flimsy than I would like. I may have to add some other reinforcement in the future. Welding to thin gauge 50 year old rusty metal sucks. My welds are embarrassing. Good thing this is the only time these will be seen. More slicing and dicing of the cowl panel and windshield frame to come soon. Next step after that will be ordering some fresh and rust free sheet metal in fastback form.
-
Yes. But sorry, forgot to post here. Truck has been sold.
-
https://www.youtube.com/watch?v=OFS14uZJdRs
-
First and foremost! It is not as nice as the pictures convey. The lighting must have been just right. I've always had a truck in my fleet the last two being 4 door duallies. Since I don't do much towing anymore I decided to downgrade, I just need a small half ton for hauling random bits from time to time. Since I can't resist cool vehicles, I ended up picking this up thinking it could both haul what I needed it to an could be a fun ride as well. I have too many other projects and as much as I dig her I need to focus on other things. More details and pictures in the craigslist ad, https://columbus.craigslist.org/cto/d/1980-dodge-d150-stepside-for/6698162653.html CR price, $3500
-
The daily driver at Bonneville.
-
I had no idea they were $1200. I had assumed a header with an issue like that would have cost far less. Great to hear they are standing behind their product and making things right.
-
Based on what I saw in your video, best case scenario, the leak is where the collector meets the primaries and a competent welder could grind back the existing weld and reweld deeper into the pocket between the primaries. Worst case, the leak is where the primaries meet and are welded to either a bullet that simulates a merge collector or a spider like in most off the shelf headers. This would require either the collector be cut off to access that spot or if lucky a pencil style tig torch could be used if the collectors are short enough. Sad to say, but a new set of headers might be less expensive than the repair.
-
Sitting on jackstands in the back of the garage. No new progress as I've been working on another project. I plan to start the metal work this fall.
-
Sold Thanks. The new owner is super excited to have found a clean E30.
-
I would highly suggest making sure whatever trailer you purchase has 5,000lb torsion axles. Leaf spring axles ride like doodoo and if it has the smaller 3,500lb. axles you can easily go beyond their capacity between the weight of the trailer, your RX7, and some miscellaneous track day gear.
-
I hate to let this little guy go but I have too many projects. CR price, $2400 Details and pictures in craigslist ad, https://columbus.craigslist.org/cto/d/1986-bmw-325-e30/6573568383.html
-
Still wonder why a man of his means choose a coupe over a fastback.
-
-
Mark, cut, try, mark, cut, try.... 6" away from contact at this point. And after a little more trimming, All of this just to locate the windshield frame and cowl. Everything else will get tossed once I purchase and fit the new roof and fastback quarter panel skins.
-
That is not far off from my plan. The outer skins will be mounted in a variety of ways. The rear quarters, roof, and taillight panel will be mounted with small light gauge tubing welded between the skins at their stronger points and shaft collars that will clamp to the rollcage and upper round frame rails. The hood and decklid will be attached with hood pins. The front fenders and apron will become one assembly that will slide on and be held with at the rear with quick release fasteners. New rocker panels will be fabbed and bolt to the sheet metal tabs that Howe welded to the lower frame rails. The door skin mounting has yet to be finalized.
-
First test fit, 24" away from touchdown before some major interference. Hacked out the stubs from the rear frame rails, some of the rear parcel tray, and two chunks of the rear quarters and related supporting sheet metal. Second test fit. Damn, still 14" from setting the rockers at framerail height. Just some minor trimming needed where the floor/firewall meets the rockers and she should finally go all the way down. I cut a short length of 1/4" round rod to the length the body still needs to come down and did a spot check on all the points of contact from the roof and rollcage and it revealed that the rollcage will fit the greenhouse even better than I first thought. Going to need some serious fender flares. I have a few good and a couple crazy ideas on how to make this happen.
-
The inner halves of the rockers had to be removed to clear the square tube outer frame rails of the chassis. And the center of the rockers had to go to slide over the door bars. I threw together a crude assembly of angle iron and square tube to keep what is left of the shell in shape. Please excuse the horrible hack job in cutting this thing apart. It is essentially a just a jig to hold the new outer sheet metal panels in place and will be scrapped along with the rest of the car once done. I'm going to light some scented candles, put on some romantic music, and see if I can get these two to mate.
-
Thanks everyone. Sure, but if beers are being consumed, I will be one of the consumers. Said beer is likely to enhance my bad decision making leading to more fabrication. Come to think of it, I think beers were responsible for the start of this project That would be excellent. This is going to be a long project though. If there is still interest when I finally turn the tires, yes please.
-
Finally getting started on this project. A while back I asked the CR collective for some help in choosing a body for my Howe chassis, http://www.columbusracing.com/forums/showthread.php?t=127749 There were numerous great suggestions and thanks again for the help. I ended up with a 68 Mustang coupe. An abandoned father son project with zero appeal to most as it is a rusty 6 cylinder coupe. To me though, it is near perfect. It has a vin tag, clear title, and plenty of new sheet metal. This weekend was straight demolition, I hope to do the first test fit to the chassis one evening this week.
-
Autocross is not racing.
-
I just picked this up for a new project. http://www.columbusracing.com/forums/picture.php?albumid=784&pictureid=8965 I only need the outer skin and the VIN tags. Everything else is for sale. Some of the larger items, Full Dynacorn floor pan, new, not installed. Fits 65-68 Mustang and 67-68 Cougar $200 Trunk lid $50 Rear glass $50 Newer fuel tank $50 Clutch and brake pedals, complete set up for manual conversion $200 Let me know if there is anything you need that I might have. It came with nearly everything that was removed when the restoration was started. Free 200c.i. inline six with any purchase... any purchase. Buy a bumper bolt for $0.50 and take the engine... please.