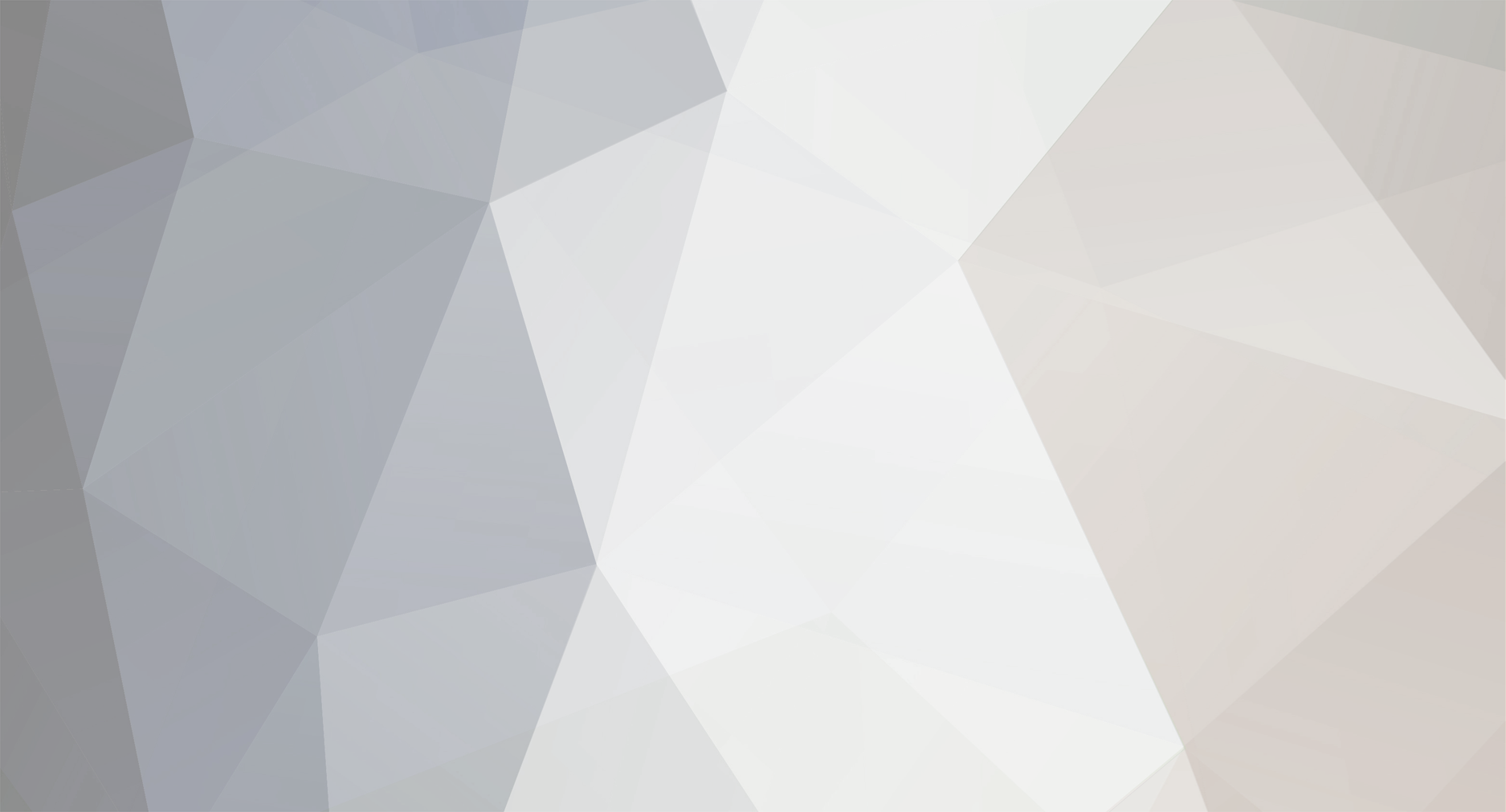
Renner
Members-
Posts
332 -
Joined
-
Last visited
Content Type
Profiles
Forums
Gallery
Store
Events
Everything posted by Renner
-
As rob mentioned, 13.0 and even 12.7 are way too lean for a street driven turbo car. I typically tune for 11.5 target during wot, with small transitions to 12.0 being acceptable. This is a proven safe limit on most pent roof chamber, intercooled turbo cars. With changing atmospheric conditions, and with not being able to re-tune your car every day, having a target of anything past 12.0 during your initial tune is asking for a melted piston.
-
You would be much better off to have the car media blasted (basically sand blasting but with small plastic particles). It only removes material in the area you want it to, leaves the raw metal surface perfect for priming and prepping, and it doesn't thin or weaken the metal structure like acid dipping does. There is a place that does media blasting near the airport, they can do whole cars, but I forget the name. They are probably in the phone book.
-
Using an average density for gasoline of about 6lbs/gallon, to convert from lb/hr to cc/min take lb/hr and multiply by 10.5. So cc/min = (lb/hr) * 10.5 or lb/hr = (cc/min) / 10.5 Edit: Damn, too slow. redface.gif
-
The bearings will last longer with the coolant lines, but you don't need them if it is a huge hassle. If you don't run the coolant lines, you should let the turbo cool down much longer before shutting it off to keep the oil from coking. That is an internal wastegate turbo, therefore it has to handle higher thermal loads then a similar sized external wg turbos. That plus the fact that mitsu needed it to last 60K miles with owners that often didn't let the car cool down at all, is why it has the coolant jacket. In summary, let it cool down nicely after beating on it, and it should last you fine. Adding an oil cooler to your system would help things out across the board as well.
-
http://www.ipsmotorsports.net
-
Since you are working on a transverse mounted V6 in a car with limited engine bay space, it will cost twice as much as you had initially thought, and it will take 4 times as long as you had initially planned. I speak from experience.... If you actually enjoy driving your car, instead of working on it all the time while it is down for 6 months, I would go with the best fitting and most trusted bolt on kit, it will end up saving you many headaches in the long run. If you can't afford it yet, spend the time working extra hours to make the money you need, instead of trying to spend the time to make your own, since the time investment needed is huge. Edit: If you decide to buy the kit and are looking for somebody to do the install, wiring, and tuning, I know just the place that can help you out...
-
I may be interested in one, but would need it to run off of 220 not 110, so that would be one less motor you need to swap out. Do you have any other specs on the lift, total height, total width, model number etc? Does it have the cross bar above the posts or on the floor? Thanks in advance. -Brett
-
Secondary Injector controllers are a horrible way to add fuel.
Renner replied to rl's topic in Tech and Tips
Of course! If you still have problems with that Honda and you are out of options, you might want to check out that HKS AIC, just might have to sell some of the other stuff. It was very straight forward, and did what it needed to do. The only issue I had with it was that the injector driver amp gave off a pretty large amount of electromagnetic interference, which messed up the spark signal on the dyno pulls, so don't put it near the ECU. If your buddy doesn't mind modding his plenum, getting the injectors behind the throttle body will help with some of the puddling that I am sure you are getting, and should improve the driveability. -
Secondary Injector controllers are a horrible way to add fuel.
Renner replied to rl's topic in Tech and Tips
Depends on the intake manifold they are being used on, and where/how many injectors are being used. I have seen more then a few late 80's 911 turbos using additional injectors to add fuel since a stock US spec CIS fuel head cannot provide enough fuel above about 1.2 bar. This is the way it was done before affordable standalones and crazy big injectors were available. I have tuned a car using a new style HKS AIC for extra fuel before, and I thought it worked very well. Was very easy to specify the starting rpm and manifold pressure. You can also adjust the duty cycle as the rpm's increase, so you can add more fuel on an exponential curve if needed. I would most likely not use one with an intake like on my Z (would actually need 2). And I would definitely not use one on any I6 intake manifold. http://images.cardomain.com/member_images/4/web/160000-160999/160293_32_full.jpg http://images.cardomain.com/member_images/4/web/160000-160999/160293_5_full.jpg This manifold came off of a twin turbo street car making well over 750 at the flywheel. 3.3L flat-6, 12 spark plugs, and 12 injectors. It is a Carrera aluminum manifold, modified to use the CIS injectors in the primary sites, with a bung for extra electronic injectors welded onto each runner just above the primaries. These were driven using an HKS AIC. This was not as insane of an engine as the one the manifold came off of. Single turbo, less boost, didn’t need as much fuel enrichment, so only 1 extra large injector is used, which is just below the throttle body on the back side of the intake in another bung. So the other 6 injection sites are blocked off. I think if you have a good enough controls system, with the correct setup on the intake, they can be a good way to get what you need. The AEM standalone for example can (among about a million other things), be used to drive secondary injectors any way that you want. All that BS being said, using a blunt tool (like a split second ARC II) for what is an inherently high accuracy application is not exactly a good way to go. Too many other factors that you cannot control can often lead to bigger problems. I would rather program up another AEM and have complete control any day. -
somebody teach me how to read compressor maps for turbos
Renner replied to smokinHawk1647545499's topic in Tech and Tips
Hope you don't have a short attention span. http://www.stealth316.com/2-3s-compflowmaps.htm -
Nope, Howard's got it covered. graemlins/thumb.gif
-
Those are the coolant pipes going to and from the waterpump to the the radiator.
-
Also check out Columbus Col-weld. They will be able to get them out without destroying the original threads, and won't charge you a ton to do it, they are in the phone book.
-
I worked at Auto Assets for 2 & 1/2 years, and having to work for Chip just began to get unbearable, so I left. I have seen him screw plenty of customers on bills, because either he or one of the techs fucked up, and there is no way he was going to absorb the cost. My Uncle is one of those customers that Chip is trying to screw because Chip knows he has money, and won't cover the extra labor time to have Gary redo the work that was done by a guy that got fired, and he still doesn't have his '88 slant nose turbo back because Chip wants like $15K more then the initial "estimate". Although he only gave him the new amount verbally, since he doesn't actually have an itemized bill of any sort It is the custom black one with red leather interior sitting in the back room for anybody that has been back there and seen it. Gary Aliff (if he is even still there) is a great guy and although he doesn't do as much aftermarket work, he knows pretty much all German cars inside and out. He also works on the side out of his house, so if you need regular mechanical work done I would suggest just talking to Gary and have him do the work, instead of going through Chip. If you need aftermarket work done, just hit me up. If any of you guys have any other questions about some of the stuff that goes on there, just send me a pm, I got to see plenty of stuff I didn't really agree with...
-
The alarm ECU is under the passenger kick panel. You have to pull back the carpet, and then remove the little wooden board which protects it from passengers feet. The EFI ecu is under there as well, along with a few other things, so check the manual to make sure you get the right one. I am am not sure if the car will start with that unplugged though. It sounds to me that you have one of the sensors that has a loose connection or something. There are trunk and hood sensors in addition to the normal door sensors. The alarm ECU should also monitor the battery voltage, so if there is something inside the car that is dropping the voltage after the car is locked, that could be setting it off. I think that there is an alarm self diagnosis, (our cars can self diagnose pretty much everything, lol). There should be a section in the manaul about the alarm system that tells you how to do it, just not sure of the page off hand. If you need any other help, let me know. -Brett
-
I agree that a step or two colder is a good idea when you are increasing boost. But platinum plugs are not bad for turbo cars. Platinum plugs last much longer then copper plugs for forced induction applications, which is why OEM turbo cars like mine come with them, copper plugs just may be safer in some situations. If you are running the car close to the edge of detonation, then copper plugs may be a good idea because the copper plug will fail before a piston melts, and may save you other severe damage if you notice it in time, whereas in most cases the platinum plug will live. So in that respect, copper plugs are safer. But, having broken spark plug pieces bouncing around in the cylinders a few hundred times before they get spit out the exhaust, and thus through your turbine blades, are not exactly a very good thing either. I do not run my car anywhere near that lean, and I don't feel like changing my plugs every 10K miles (which I would have to with copper plugs due to the wear), so I run NGK platinums for now. If I were building a high power turbo motor running 2 bar all the time, then I would probably run copper plugs. But for most street cars not running insane amounts of boost, and with a reasonable tune, platinum plugs may save you some headaches, especially if they are a pain in the ass to change like on a VR4.
-
LOL. Now this shit is getting funny.
-
Hey Brian, the Type-R BOV will have some "flutter" to it, which will sound like a very loud surge. Since the valve itself has a very large range of motion to be able to move so much volume, the valve will open and close several times during the vent process, causing the "sneeze" type noise. This is most likely coming from just the cycling of the BOV, and not surge from your turbos. Basically, there is pretty much no way you are actually getting more compressor surge with the type-R BOV then you were getting with no BOV at all. If you want, you can just give me another quick ride so I can see how she sounds.
-
Here you go: http://www.stealth316.com/2-awd2.htm#Transaxle http://www.stealth316.com/2-awd3.htm#cdvcu These cars have been tested to have anywhere between 25%-30% driveline loss when tested on an engine dyno, and then on a split roller chassis dyno (where the rollers moved independently). That is the key point, because the viscous coupling is required to transmit max power for a split roller setup, and thus the car will have the max driveline loss in this case due to friction and gear loading. So basically when you are out doing a highway roll, you will not be losing the full 25-30% unless you have wheel spin, but how much you are losing has not been calculated or tested yet, I would assume it to be closer to 20-25% instead based on some results from other AWD systems. The 6-speeds hold up better to abuse then the 5-speeds. BTW, the AWD system in the Porsche 993TT will transmit 95% of the power to the rear wheels until slip is detected, and only adds a total of 93 pounds to the total vehicle weight.
-
You are missing the point of what I was explaining. As I said in my second paragraph, of course the complete setup specs of the engine all sum to aid or hinder pre-detonation control, I never even implied that they didn’t. But when you said that the CR of the engine is meaningless when it comes to an engines ability to run boost safely without pre-detonation, then that is where you are incorrect. The other factors are only a very small percentage of what causes the elevated cylinder pressures and temps that actually allow for the combustion process to take place in the first place, or which may push the engine past the point of safety. That is why we use compression in the first place...... If the CR of an engine didn’t matter in terms of temperature increase, and thus possibility of knock onset, why are you even mentioning what CR you will be running on the new engine? Why not just build the aluminum head motor with a 13:1 compression instead, since the CR obviously doesn’t matter for knock control, and since you have taken all of those design measures to help combat knock? Also, how can you possibly know the true CR of an engine you haven’t built yet? You can’t, you have to use the numbers given with a certain target CR in mind to begin your build process. You design the engine for the target CR first, and then modify the remaining parameters from there based upon your tolerance at that CR, or make small modifications to reach the desired CR. How can you know the volume of the combustion chamber you want without knowing what kind of CR you are even aiming for? It sounds to me like you are quoting the given numbers for only the pistons that you plan on using. That is not the CR. Is that how you determined the CR of the first engine also? You cannot know the actual CR until the piston and combustion chamber volume are measured and calculated together. How can you try and predict what octane the new engine will run on until you have done it yourself, here in this atmosphere in good old C-bus? If you built an 11:1 NA engine that knocked on 94 octane, then there was something significantly wrong with your setup/tuning, hence my comment about having a stock internal engine(which is what this thread was supposed to be about), where the quench volumes for example were still intact per the designs of the GM engineers. Do you know more about combustion dynamics then the guys who designed those engines from the ground up? I know I sure don’t. And I am willing to bet that there are plenty of similar setup 11:1 CR engine around that had zero detonation problems. And yes, the CR of an engine is in fact dynamic, not static. So if you want to talk about the actual CR of an engine, calling it static is not correct. You may be referring to the theoretical CR of an engine, which is what the numbers given to you by the piston/head manufacturer are. Then there is the measured max CR of an engine, which is what you find when you CC the combustion chamber, etc. These are the numbers we are supposed to be discussing here, because those are the numbers measured and listed by the engine manufacturer. But the actual CR of an engine, which is what I stated was the “single most defining factor to the ultimate combustion chamber pressure” is in no way static, because it is rpm dependent among many other things. Come on Mark, I would have expected you to know this! This is a very difficult array of numbers to figure out, and requires some extensive testing of an engine, but it is also the most useful. Since pretty much none of us here will ever do the data compilation for the actual CR number (requires a serious research environment), then the closest thing we can go by is the measured max CR. This is a good assumption, since the actual CR is a completely reversed harmonic process, offset so that the upper bound wave limits lie just slightly above the measured max values, but with the lower bound wave limits well below the measured max values. BTW, you don’t need to work on Porsches to be a guru, but I would assume that such an expert engine builder who has been doing it since 1988 would be a bit more adept at doing some of the work on his own car, like changing spark plugs, replacing suspension pieces, etc.... tongue.gif
-
Ahem, reading a bunch of books or internet threads about engine building doesn’t exactly make you a guru either. tongue.gif Actually, I am going to have to disagree, where did you come up with this theory anyway? The compression ratio is the single most defining factor to the ultimate combustion chamber pressure, and should be the very first parameter used to base the performance capabilities off of, for a given bore, stroke, and rod length. How are you going to figure a combustion chamber temp, and thus an engines ability to resist knock, based on the fillet size used on the piston dome for example? Also, it is very difficult to change the quench volume to the point of excessive out of control pre-detonation without significantly influencing the CR, so in this aspect, with a stock internal engine (no monkeys making changes to quench area), the CR should once again be referenced first and foremost. I wouldn’t exactly refer to the CR as static either, since it is anything but static. The number you are referring to (9:1 for example) is actually the maximum CR seen during the cycle, and could only be considered static if it were constant throughout the combustion process, which it is not. I do not consider 9:1 a high CR at all, several of the NA engines we built at Auto Assets were running 13.75:1 or more for compression ratios for endurance engines, and on regular old Turbo Blue leaded. Those numbers I consider high. The other things you mentioned are of course causes for perturbation points of pre-detonation, and should always be taken into account when designing a better engine. But they are not the defining factor to what kind of cylinder pressures the engine can handle when running correctly, or if it could be converted to FI or not. They are actually a very small percentage of cylinder pressure and temperature fluctuation when compared to the total amount of temperature and pressure change from the compression and combustion processes alone, but which usually are the small things that push the thermodynamic process over the edge past the point of safety. For example, if he has iron heads, he should run a better intercooler to lower the charge temp, not swap the heads for an aluminum pair just due to their better heat transfer coefficient, because it will be a much smaller percentage change in cylinder temp/pressure when compared to the difference made by the lower charge temp from the better intercooler. Aluminum having a better heat transfer coefficient isn't the deciding factor in head materials either, steel has a higher thermal capacitance then aluminum, which is a very good thing in certain cases. The CR is the same in this way, lowering the CR (if needed), and thus changing the piston shape, will give you many more benefits in terms of pre-detonation prevention then changing the shape, material, or valve size of the head will ever do. The ideal piston for a quench type chamber would be a flat top design, which did not have any kind of dome protruding into the head chamber, which of course dictates a lower compression piston just due to the flat top shape. This reduces the area of the piston head to a minimum, reduces the amount of combustion heat absorbed by the piston, and eliminates combustion inconsistencies created when there is a large cone section separating the chamber into irregular cavities. Any sort of piston dome will cause compromises, since the flame front cannot spread smoothly throughout the chamber. A low compression engine is going to have more of a flat top type piston, good for pre-detonation prevention, and a high compression engine is going to have a dome shaped piston of some sort, prone to pre-detonation issues. Soooooo, the compression ratio tells you way more about the internal geometries of the combustion chamber and its capabilities then you think, because the CR is almost completely governed by the shape of the piston, assuming you haven’t done anything wacky with the combustion chamber and quench area (which he hasn’t on a stock engine). With the proper tuning (i.e. timing, fuel, no excessive backpressure, etc.) and an efficient enough intercooler, (low enough charge temp), I don’t see any reason why you couldn’t run 15 psi on bone stock internals with no knock on almost any car with a 9:1 CR, assuming your internals were strong enough to handle the loads of course. [ 06. June 2003, 02:30 AM: Message edited by: Renner ]
-
Moving to Tech....
-
Hey Scott, check your pm.
-
Hey Scott, there are a few things I would try: First I would pressurize the system to find any and all leaks. Howard still has the coupler that I made for my car, but I am sure it will be too big for yours since you have two smaller inlets instead of one large one. Your turbo inlet pipes are ~2.5” correct? It only takes me about 5 minutes to make one, obviously for yours I would need two, so just let me know what the actual pipe size is if you want me to make them. By pressurizing the system on my car to only about 7 psi, I found 3 vacuum leaks, and one MAJOR boost leak that I could not have found any other way, because the clamps all seemed nice and tight. It is easy to do, just hook it up to an air hose, and find where all the hissing noises are coming from. You could possibly have a leak somewhere other then a silicone fitting that could be venting boost, like maybe a crack in one of the intercooler end tank welds or something else that isn't an obvious problem area. If you don’t find any boost leaks, I would check the wastegates next. I have access to a small spring tester here, so we would have to remove the wastegates, take the springs out, and see if either or both are getting weak. After enough extreme heat cycles (which wastegates see plenty of), any spring will start to loose some of its force ability. It would be pretty easy to look for any tears of the wastegate diaphragms while they were apart as well. Checking out the bearings in the turbos would be a good idea too. A failing bearing won’t allow the turbo to spin up to as high of an rpm, so it will not build as much boost as it should. You can check this by driving the car to get it up to normal operating temp. And then shutting it off, and removing the inlet pipes. You can spin the wheels by hand by using your fingers on the locknut. They should remain spinning for several seconds under their own inertial forces. I have seen some ball bearing turbos remain spinning for over 30 seconds after shutting the engine off while it was just sitting at idle. If one is bad enough to limit your boost level by that much, it should be obvious. I am pretty sure you can rule out any exhaust manifold leaks. Anything that large would be very noticeable. Lastly I would do a compression test on the engine. You never know, it may be getting a little blow-by after all of the miles of high boost. If the engine is starting to get soft, you may have gotten to the point where you aren’t holding/creating enough compression to maintain that boost level. I think this is pretty unlikely, because you would notice it gradually starting to get weaker, but it is easy to check, and it is always good to know if you have a cylinder you should keep an eye on. If you want me to make those couplers, just let me know, I could probably do it early next week, and they only cost a few dollars each, so making them is really no big deal. I may actually have time to screw around with cars this weekend, so I will probably be over at Jeff’s working on the big white paperweight if you want to swing by, your turbos are so easy to get to it would only take about a minute to check out the bearings if you want a second opinion. See ya. -Brett
-
I don't think you should have much to worry about in terms of matching the exact fuel pressure you had with the stock regulator. Not 100% sure about the older ford motors, but most of the turbo cars I am used to working around at least, usually run around 47 psi base fuel pressure with the vacuum line disconnected, on a regular 1:1 rate regulator. So with the car at idle, and the vacuum line hooked up, your rail pressure would drop maybe 10 psi below that, depending on your car of course. If you are going to be doing some fuel tuning anyway, you can just adjust the injector pulse width to get things where you want them. Basically, A 3 psi difference in the rail pressure is not going to make the difference as to whether or not the car starts and runs ok. Unless one of our local ford gurus speak up, I would say that 45 psi, for a no vacuum base pressure at idle is a pretty safe starting point.