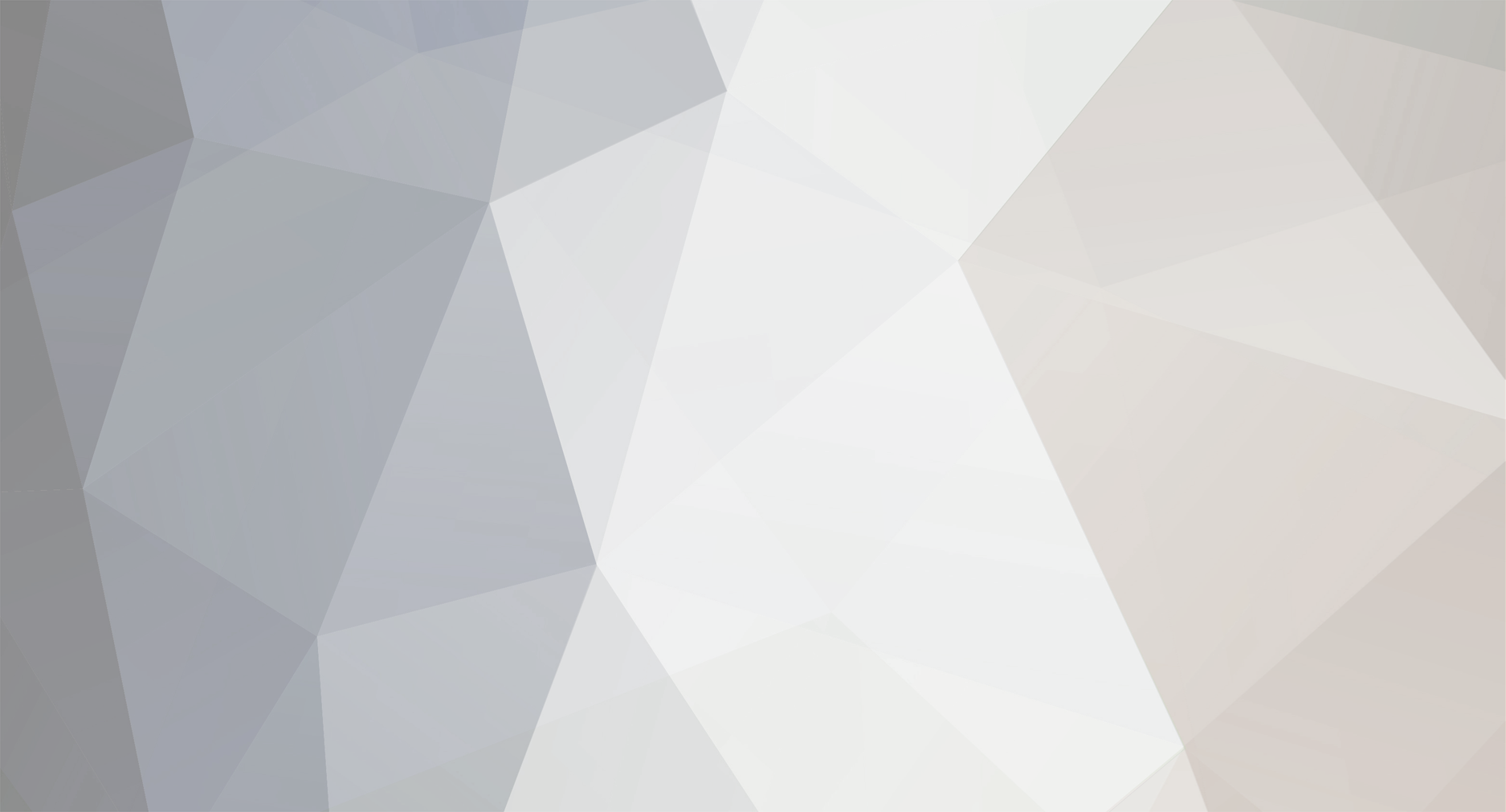
desperado
Members-
Posts
1,239 -
Joined
-
Last visited
Content Type
Profiles
Forums
Gallery
Store
Events
Everything posted by desperado
-
Those motors tend to have alot of piston slap (2.0) It could be that, or possibly to mechanic left something in the motor when he put it back together.
-
Well the same ones that came out of it of course. If that is the answer, don't do it. Go buy at least new stock bolts, or better yet ARP studs.
-
Yes, I still have the motor. Call me if you want to take a look at it or if you need additional information. 740-967-4324 Trades will be considered
-
Anybody running an MSD retard box that takes modules? I need to get the resistance readings on some of the modules (the little pill things are really just a .05 resistor in a cool little pill thing) I can't see buying these things for the price that they want for em, and I would be glad to share the information as well as the info on the MSD RPM limiter pills I have, they are also just a cheap resistor in a pill thingy. With the RPM info I can build up either a pill at whatever RPM you desire, or make a variable pill and show you how to set it with a digital meter. Check out my posting about what I did in the camaro for a better idea of what I am talking about.
-
As far as I know it does run. It is very clean internally, feels good turning it over, you are more than welcome to come look at it. I am in Johnstown. Call me at 740-967-4324. I am between jobs right now so I am around all the time.
-
Not sure what you are experiencing. It sounds like a maybe a motor mount. Car seems to rise up in the front under accleration right?? FWD Drive Dodges seem to have that feel to them But I would check the mount. Is it a 4 or a 6 cyl BTW??? Reason I ask is the 3.0 liter tends to tear the rubber in the mounts up pretty regular after 70000 miles of so. My Chrysler TC is horrable about that, and the car squats down in the back, or at least it feels that way. Hope this helps. To the others and there silly posts. Remember that at one time, you were a noob too. See my sig if you have any questions.
-
Last Bump I now have the rails, injectors and computer. Only thing needed to get this together is the in car part of the harness. Price dropped, $300 or swap for a wet nitrous kit. Looking for a plate kit for a 4150 Holley (square bore) but I can work with whatever.
-
Having some background in electronics, I know this can be done. But I can't pull this off myself. Here's my idea. These days there is a little black box for everything, turbo timers, boost controllers, delay boxes, nitrous progressive controllers, and the list goes on. So how about a multi stage progressive nitrous controller and ignition system that had accelrometers in it for traction control. I see these Traction controls on E-bay that look like a 6AL MSD box, and assume that the theory is they are looking at rapid changes in RPM and consider that to be tire spin and retard timing. Which of course will limit power and control tire spin. So I want to take this further, accelrometers will sence changes in forward motion, accelration basically. If you spray, especially alot, traction is difficult at times to achive. And alot of spray requires timing to be retarded anyhow. This is why I say put the ignition system in the controller box. If it's microprocessor controlled, it can be tuned with a laptop for the base line timing, timing curve without spray, degrees of retard per stage of spray so if you start out spraying a 100 shot and stage 3 is a 200 and you deside to rejet to 300 the controller can be changed. So far this all exists, MSD can do all this stuff. But, if you link not only the ignition system in but the acclerometers, then you can also control the stages of nitrous progressively to eliminate wheel spin. Basically the software would continually look for changes in RPM, throttle position and accleration. If there was an extreem change in RPM without the accleration changing to a degree similar to the RPM change it would retard timing, or if spraying, would progressively lessen the spray, or eliminate it untill the tire spin has ceased. And this would all happen while the driver was still pedal to the floor. If there are some devry guys in here, this would be a kickass senior project to undertake. There is obviously a market for something like this, with the import craze, front wheel drive cars are not great with traction, adding a 250 shot to a FWD car and traction is non existant. RWD cars would benefit from this greatly too, A top notch lower end motor, with conservative fuel curve for around town ecomony and 600 HP of spray that wouldn't just melt the tires. Yes, it's a tall order, but quite possible, it's just finding the right person to get it together and working. Anyone up to the challenge?
-
Help me understand how an in-line fuel pump pumps more fuel...
desperado replied to excell's topic in Tech and Tips
He He... around and around we go. I found two things after re-reading this all about 5 times. First is, I can be an asshole. graemlins/asshole.gif But we all knew that, and to all of you that read all of this trying to dycypher the actual theroy that I clouded with being an asshole, sorry. I do still stand firm on the two pumps thing, and what Don said helps to demonstrate it. If you take a garden hose and hold it with nothing on the end, the water will only go a few feet out. But stick your finger on it, the water goes alot farther, now think about what you have done. You have increased the pressure in the hose, but you have decreased the volume of water flowing in gallons per minute from that hose. Now with watering your garden that's not a problem. In a fuel system decreasing volume is bad because less volume of fuel gets to into the engine. So so increasing the restriction, which would be leaning out the motor, in effect turning down the flow, but not the pressure is bad. Now, a motor needs two things from the fuel system, a certain volume of fuel needs to erach the injectors. But that needs to be at a specific pressure. So everything else being equal, if we want the open hose, to shoot the same ten feet that it will when there is no finger over it. What do you have to do. And Ricky, you are on the right track, you have to increase the pressure in the hose. Now at this point ther seems to be no restriction in the hose, but the hose it's self is the restriction, by itself. Follow this real close (no I ain't being smart assed either) The internal restriction of the hose, is the injector so to speak, it can't be changed to flow less or there isn't enough fuel in the motor to make the mixture right, even if the volume exists in lph, ot GPH, the pressure is too low. So it is not right, so to make it right. To get the water to come out of the hose and spray ten feet, with out restricting the end with your finger. You have to pump enough water through the hose until the restriction of the hose itself starts to create to pressure necessary to shoot a larger stream of water than the stream with your finger over it (more volume) the same distance. I wish I come explain this better, I can demonstrate the heck out of it, but that ain't gonna help here. It need to be done in person. Lets leave this alone. It's to the point that we need to agree to disagree and forget it. -
Seen em jam with stop leak. I know that you would never use stop leak because it plugs up radiators, heater cores and such. But has someone else in the past, say a previous owner done that. And you need to test the stat, take a pan of water, and a themometer that will go to 250 degrees. Put the stat in the pan with the water, and heat the water, when the water reaches the stat opening temp, it should open (180 to 220) it will be stamped on the stat some place. If it opens then you have a different problem. I would say either a clapsing hose, or a partly clogged radiator.
-
Help me understand how an in-line fuel pump pumps more fuel...
desperado replied to excell's topic in Tech and Tips
As far as the injectors being too small, I assumed that if he's running out of flow with a 255 pump the injectors are not stock to begin with. I didn' say that though, but I did figure that was the case. That being said, as far as the flow issue, that is what I was saying all along. If you are requiring more flow than the pump can provide, pressure will drop. Adding anything that brings the pressure back up to acceptable levels without changing the current restriction has to increase flow. So putting an inline pump in, if the pressure comes back up, the flow has increased. -
Help me understand how an in-line fuel pump pumps more fuel...
desperado replied to excell's topic in Tech and Tips
RL... the voice of reason... thanks. As far as the comment I made about increasing the fuel pressure in a return line regulated system. That was a rebuttal to a comment made by someone that said that running an inline pump would run the pressure to high. And what I was getting at was that the only way that the fuel pressure whould get too high is that flow rate would have to increase to the point that the regulator could not flow enough fuel back in the return to keep the pressure in check. But I don't think that is going to be the case with just adding an inline pump. I also saw that someone said that increasing the restriction of flow would increase pressure. But that is of course counter productive in a fuel system. To make a specific amount of horsepower, you need to convert X number pounds of fuel per hour into heat energy, which the engine converts into mechanical energy. If you restrict the flow of fuel the power has to drop. But I think that everyone understands this. The whole idea of what we are doing is increasing power, which requires more fuel. Not sure how we got from where this started to here, but it's been a fun trip. -
The only difference in forged pistions and cast pistions is toughness. A forged piston will take more abuse, AKA more spray. As far as changing the computer, unless you increase the bore, or change compression ratio you will not need to reprogram the computer. The motor will remain the same as it was, but be able to take more abuse from the spray. Hope this answers the question.
-
Help me understand how an in-line fuel pump pumps more fuel...
desperado replied to excell's topic in Tech and Tips
Well you did and you didn't. By adding the second pump you were maintaining pressure, but in reality, you were increasing it, from where it was low back to the standard level. And to do that, you increased the flow. You were doing it to maintain pressure, because your fuel flow requirements were greater than the single fuel pump could flow and maintain the pressure. Look at it like this. A power washer pumps water at a very high pressure, anywhere from 2000 to 3800 PSI, through a small orifice. That is fixed. It you take off the orifice (nozzle) the pressure drops drastically. The reason is pump is designed to build a certain pressure at a given flow. By removing the nozzle you increase flow capacity. Same thing happens when you increase pulse width on an injector, it is open longer, and flows more. Now if it flows more than *** pump that supplies it can pump through and maintain the rail pressure, it will drop. The only way to get the pressure back up is to increase flow. Because the flow requirements have changed. Pressure is a restriction of flow. I wish I could explain this better, but that is as good as it gets with the online explanation. Catch me at Geeros and I will go deeper for those that want to know. -
Help me understand how an in-line fuel pump pumps more fuel...
desperado replied to excell's topic in Tech and Tips
Doug said : When I had my inline it was more to take some strain of the intank pump and help keep my pressure up. Didn't actually flow anymore amount of fuel. As did the man with no name made a similar statement. Sorry, but ERRRRRRRRR. you missed the ten million dollar question. If you are pumping a fuild, and it is a balanced system, and you increase the amount of flow at the outlet until the pressure falls, you MUST INCREASE FLOW in order to reestablish the original pressure. There is no way around this. So if putting a second pump in line does increase your pressure, it does so by increasing flow. And in a return flow regulated system, there is constant flow, the pump is never dead headed (pumping against a closed system) the regulator does its job by passing enough fuild back to the reserve (gas tank in this case) to maintain the pressure in the system. Laymans terms, if you build your shit to take so much fuel that the pump can't maintain pressure you have to put a pump in that will FLOW more fuel in order to restore the pressure you had. Did a full year of fuild power and fuild dynamics in college. Focused on mostly hydraulic systems, but it is all one in the same when it comes to basics. Now the ONLY WAY to increase pressure of a return flow system, is to either readjust the regulator, or to put more flow in the system than the regulator system can bypass. If this is done in a fuel system it will just burn up the pump/s. And pressure will be very high until pumps fail. If you do it with a hydraulic system, it will burst the weakest link in the system, but a hydraulic pump is designed for 5000 psi at a specific volume. Been there, done that and got soaked with 20 gal of hydro fuild. [ 17. February 2004, 04:57 PM: Message edited by: Desperado ] -
Help me understand how an in-line fuel pump pumps more fuel...
desperado replied to excell's topic in Tech and Tips
I just read your reply, and saw your fuel flow requirements. Just sticking an inline pump in will help for a while, but it's a bandaid at best. V-6 needing over 255lph, my guess is it's a turbo and you are spraying it to boot. Just guessing at this point but that is alot of fuel. Your lines, if factory are going to become a restriction here real quick, if they are not already. So you might want to start considering a major rework of the fuel system. If you are spraying, you can run a seperate fuel system and pump for the spray, and that will take some of the load away from the primary system, The other thing this enables you to do is run better fuel with the spray, but I don't know for sure that you are spraying, but that is just alot of fuel requirement to not be. -
Help me understand how an in-line fuel pump pumps more fuel...
desperado replied to excell's topic in Tech and Tips
Fluid Dynamics 101 Two reasons. As far as flow, first thing is that you loose flow by presurizing the outlet of any pump. If you have two pumps in a line the first pump does less work and therefore can pump more volume because it has less pressure on the output side due to the second pump in the line. The second pump does not have to work as hard to created to same amount of flow because the inlet is pressurized and not at a vacuum like the first pump is, or any stand alone pump will be. The other reason, and it seems more to what you are asking is that most pumps do not restrict flowthrough, by this I mean that even with the pump turned off, if fuel is sucked through it, it will allow fuel to flow. Most tank pumps are turbine pumps, sort of like a turbocharger, of course a turbo will flow air through it even if it's not to speed. Now the other the thing that happens it the two pumps share the load. Neither of the pumps does as much work as either would do alone. The tank pump does not have to work against the same pressure on the engine because there is a second pump sucking fuel into it and pumping it on to the motor, the second pump does less work because the inlet is pressurized and it does not have to build as much pressure to ge to the required prussure. This also applies to flow. Now if you are wanting to do this right, there are some sizing considerations but just sticking a pump in line is going to help. I don't know what you are feeding or what your plans are, if you need some more info let me know. Hope this helped. -
last bump. $500 or reasonable offer. Will trade for wet kit, or Chevy performance parts. This needs to go, Need the money for my other projects and the room to do them.
-
Hmmm, that is alot of welding, as far as the rods. I have 20 lbs of it in the garage now. But cast has to be heated or it will crack from the welding heat. Another way to do what you are wanting to do is to braze a piece of metal in there. As far as the epoxy's. There are a few that guys use it drag motors in the exhaust tract. But not a street motor. Reason is that the heat cycling is alot greater, and that tends to crack the epoxy.
-
The light problem is most likely in the turn signal switch. I have seen this in other cars and that was what caused it. As far as the idle problem. If it died, did you have to jump it to get it to run again? If so I would say that the alternator might be a little weak, and when it was idling it was not making enough power to keep everything powered up. That is the first stuff that I would look at.
-
It can be soldered, I have done it many times, but you need a fairly hot iron that will do it quickly, a hotter iron actually keeps the heat more localized because it takes less time to do the job.
-
Did they break at the ends, or in the middle?
-
WAIT,,,,, F*CK.... I just reread the post. You are talking about the camshaft not the crank. In that case. you can't weld it at all. just replace the thing. If you need some help get with me.
-
I am not sure that I follow you. I get the notion that you broke the snout off the crank or something like that. That can't be fixed. Welding a crank is done if you have spun bearings and screwed up the machined areas (rod and main journals) of the crank. Then the crank will need to be turned back down to size and repolished. This is a vrey expensive undertaking and pretty much reserved for high dollar racing cranks that cost thousands of dollars. Not for stock cranks. Just the welding part would be more expensive than a new crank. Then the machine work would add to it. But if you broke a crank. Either of the ends, or in the center, it's junk. and there is nothignto be done with it other than shit can it and get a new one. I know that those SHO motors will turn mad RPM's and are known for breaking pulleys, if he pulley is broke but the crank isn't damaged just replace the pulley. If you aren't sure what's going on with it. Get me or someone to stop over and take a look that knows what to look for. It may not be as bad as you think.
-
You would have to talk to Tinman to be sure, but I think that M&M does that. Just wonderin, why not just replace it. I have found that ERS and the other similar places, it's cheaper to buy a recon crank with bearings than it is to just get one turned.