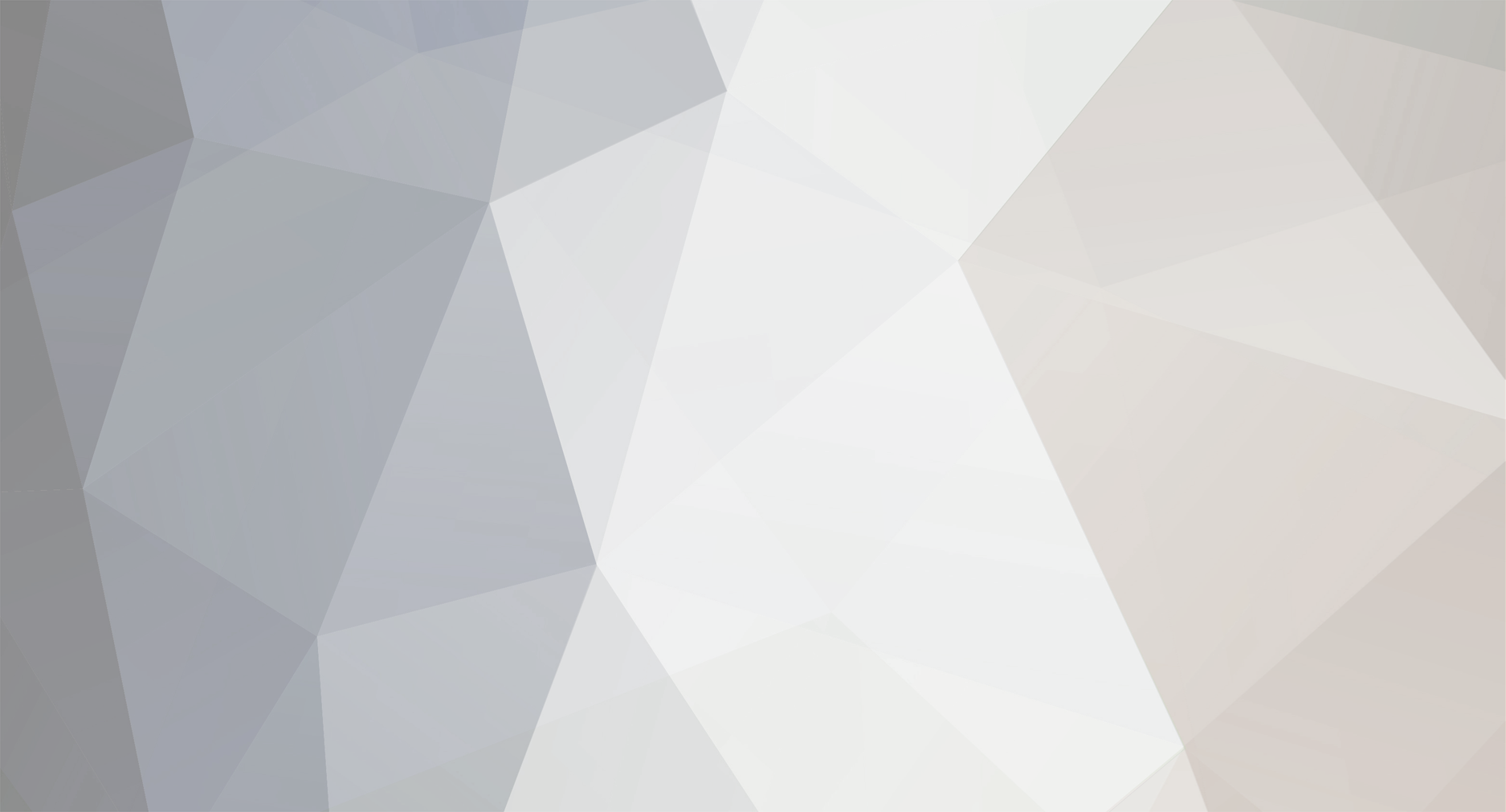
SupraGlue
Members-
Posts
679 -
Joined
-
Last visited
Content Type
Profiles
Forums
Gallery
Store
Events
Everything posted by SupraGlue
-
Found this on a site that sells cryo treatment. Take it with a grain of salt, but it explains in a metallurgical sense what the cry treatment is attempting to achieve: http://www.300below.com/cuttingtool.htm "Chilly Changes Slowly cooling a tool steel to deep cryogenic temperatures and soaking it at this low temperature for several hours changes the material's microstructure. Almost all of the austenite (a soft form of iron) retained in the steel after heat treating is transformed into a harder form, martensite, by deep cryogenic tempering A second result of a deep cryogenic "soak" is the formation of fine carbide particles, called binders, to complement the larger carbide particles present before cryogenic treatment. (Depending on the alloying elements in the steel, these particles might be chromium carbide, tungsten carbide, etc.) One recent study by Randall Barron, Department of Mechanical Engineering, Louisiana Polytechnic Institute, Ruston, LA, looked at how the changes brought about by cryogenic treatment affected steel's ability to resist abrasive wear. This type of wear occurs when a body penetrates and gouges a material's surface. The gouging body may be a surface asperity on a mating part, a freeabrasive grit particle from an external source, or an internally generated wear particle The Barron study found that the martensite and fine carbide formed by deep cryogenic treatment work together to reduce abrasive wear. The fine carbide particles support the martensite matrix, making it less likely that lumps will be dug out of the cutting tool material during a cutting operation and cause abrasion. When a hard asperity or foreign particle is pressed onto the tool's surface, the carbides further resist wear by preventing the particle from plowing into the surface. Some of these benefits may be achieved through standard tempering, which also transforms austenite into martensite. But standard tempering may not bring about a complete transformation in some tool steels. For example, 8.5% of an O-1 steel remains austenite after it is oil-quenched to 68'F. If M- I is quenched from 2228° F to 212° F, then tempered at 1049° F, the retained austenite is 11 %. Additional improvements in tool performance can be achieved if this retained austenite can be transformed to martensite. As Barron's study has confirmed, adding a cryogenic step to the treatment process does just that. In the chart accompanying this article, data drawn from another study of treated metals by Barron indicates which samples exhibited improved abrasive Critics In addition to examining cryogenic treatment's effects on austenite transformation, Barron also looked at other, less obvious metallurgical changes. His data helps answer those critics of cryogenic tempering who doubt the effectiveness of a process that imparts so few visible changes to the metal. These critics say heat treating already changes 85% of the retained austenite to martensite, leaving only 8% to 15% to be transformed by deep cryogenic tempering. Using the process to produce such small results is inefficient, according to the skeptics. These observations are accurate as far as they go. But they fail to take into account the fact that metals subjected to deep cold develop a more uniform, refined microstructure with greater density. The particles that are formed through the precipitation of additional microfine carbide fillers take up the remaining space in the microvoids, resulting in a tool steel with a much denser, coherent structure that improves wear resistance. Metallurgists have known that cryogenic tempering has this effect, but they may not have realized the extent to which the microstructure changes. Researchers in a study conducted at the Jassy Polytechnical Institute in Rumania used a scanning electron microscope equipped with an automatic particle counter to identify and quantify these smaller particles. Through this examination they found that cryogenic tempering creates a significant change in density throughout the tool Some people acknowledge the benefits of cold tempering, but they question the need to use temperatures below -110° F. A review of the data from the Barron study, however, shows that some tools, at least, perform significantly better after processing at-310° F than they performed after -110° F tempering. Among cutting tool steels, for instance, the wear resistance of M-1 HSS was almost one-and-a-half times the wear resistance of the untreated material after a-110° F soak. After a-310° F soak, the steel exhibited two-and-a-quarter times the wear resistance of the untreated material. T-1, the traditional tungsten HSS, went from a little under one-anda-half times the wear resistance after a -110° F soak to one-and-three-quarters the wear resistance after a -310° F treatment. It may be concluded from these tests that treatment at -110° F does improve wear resistance, but deep cryogenic treatment at -310° F improves wear resistance much more. To allow time for the very fine carbide particles to form and the retained austenite to be transformed into martensite, a long soak at deep cryogenic temperatures is necessary." Ultimately, it would seem to come down to a cost-benefit analysis. Does the extended wear life of the part(s) in question justify the cost of the cryo? [ 15 December 2002, 02:48 PM: Message edited by: Stolen UFO ]
-
Everything I read from the Supra road racers indicates that it extends rotor life. Several of them swear by it and won't use non-cryo rotors anymore. I have never read a real engineering breakdown of why it works, however. Cold fusion mumbo-jumbo, or high-tech mojo? Try it and let us know. tongue.gif
-
I used the formula: hp = (flow rate * number of injectors * duty cycle) / brake specific fuel consumption For flow rate, I used 35 lb/hr, which is just about right on for 365cc. For BSFC, I used .5. This may be a little optimistic. For duty cycle, I used an absolute max 90% since he's talking about top feed injectors. Knocking off 10-12% driveline loss estimated for a manual, you end up around 220-225 at the wheels. The only way to know for sure is with tuning, but I'd say that without jacking up fuel pressure, my best guess is that the four 365cc injectors aren't going to safely give much past 225rwhp.
-
By my math, it looks like those injectors can flow enough to get you safely to around 225rwhp. Anything more, and you're looking at some kind of fuel system. For the power level you want (350), you'll need to upgrade to ~550cc injectors. A single Bosch or Nippondenso (e.g. MKIV) fuel pump would get you enough flow. Used Supra pumps can be had fairly inexpensively, and I'd run an AFC to keep fuel control simple and cheap. Sounds like the supercharger isn't doing a hell of a lot. Any idea what stock boost was? As far as the different motors, it depends on how much boost you plan to run. I'm tempted to think that the 8.9 CR one would be a better choice if you went turbo only, due to better off boost performance. A decent intercooler (Isuzu NPR or Starion or even MKIV side mount) should keep it out of detonation up to a moderate boost level on pump gas. EDIT: Just read your edit. If the 3S is a straightforward swap and you can get one at a reasonable price, I would totally do that. Great motor, and easy on upgrades. The sky is the limit with that. [ 13 December 2002, 11:50 PM: Message edited by: Stolen UFO ]
-
The 4A-GZE swap makes more sense, then. That price is decent considering the power upgrade it represents. If twincharging proves to be too complex, it's always possible to remove the supercharger and just run a turbo if you get bored with the power level. There is probably some custom fabrication involved if the parts don't already exist. What size injectors does the GZE come with?
-
How much can you get the 4A-GZE for?
-
HKS used to make a turbo kit for the 4A-GZE. It's out of production now. Some of the parts might be hard to find, but if you really wanted to do that, it would be the way to go. I'd go with what Jess said. Turbocharge the 4A-GE. To get to over 300hp, you'll still have nice spool with a T3/T4. Strip some weight out (no, rust does NOT count tongue.gif ) and you'll be all good. I'm sure you can find a used 4A-GE to build/rebuild while you have your current one still in the car. Once the new one is built, swap it in and you're set. Don't forget to budget in a clutch.
-
What you want is a sequential turbocharging system like a Supra or RX-7. Unfortunately, engineering one might be more expensive than simply buying a car that has one. There have been some experiments on what you are trying to do -- it is called "twincharging", and there are a few websites out there describing it. I'm not aware of any that I'd call 100% sucessful just yet that were home done. HKS did a turbo kit some years back for the Supercharged MR2 (the reverse of what you are wanting to do), which I don't know too much about. It's been off the market for a while Theoretically speaking, you'd probably want to blow the supercharger output into the turbo intake, but also have a one-way bypass valve (maybe some kind of reed valve) to allow the turbo to draw air in when it surpasses the flow capacity of the supercharger. There should be no need to declutch the supercharger in that case. This would also allow you to run the air from both the supercharger and turbo through the same intercooler. If you did it the other way around, by blowing the turbo output into the supercharger, you would run into two problems: first, the turbo compressor housing would be an inlet restriction, and second, the turbo boost would possibly have a tendency to blow past the seals of a roots-type blower. Search Google for twincharging and you'll find some people who have tried it.
-
If you could pick any positive displacement supercharger...
SupraGlue replied to excell's topic in Tech and Tips
witha name like that we'd have to make fun of you chris lol </font> Nah. We'll just make fun of YOU when he beats you with his four-door family car. "Ha ha. Chris just Whipplecharged Berto." graemlins/gay.gif -
If you could pick any positive displacement supercharger...
SupraGlue replied to excell's topic in Tech and Tips
Autorotor 2.3l blower. Because swedish chicks are hot. ill second that. kenne bell of course..dont they use autorotors[/QB] Yes, as does Whipple. Unfortunately for Chris, there doesn't seem to be an application listed for the 3.8. -
Tommy, your logic is flawed. White Castle is still in business after 70 years. tongue.gif
-
It doesn't surprise me that Ford's own Motorcraft filter is very good. Toyota makes excellent filters also. Oddly enough, OEMs seem to know what they're doing.
-
For any compressor map junkies, this is COOL. http://www.turbofast.com.au/turbomap.html
-
With as much salt as ODOT uses on the roads, I'd say stainless is a smart purchase. It's also lighter.
-
Also look at the BFG G-Force KDW2. Nice rain tire, great dry traction and they seem to be lasting a while. They should be under $150 in that 17" size. The KDW2 has a nice agressive-looking tread pattern also. Cons of an 18" wheel are going to be stiffer ride (which could also be a "pro", if you view stiffer ride as better road feel), a little less launching traction and more likely chance of bending a rim on a pothole. Pros are going to be better looks, and sharper turn in response. Depending on tires, your max lateral g's may go up also. The primary reason to go with larger rims, IMO is so that you can fit larger brakes underneath them.
-
Eric is GONE!! Now, who wants to throw rl's Lightning off?
-
Read the thread, it was already updated.
-
Updated to a full top 25. Boost Me and Tank didn't make the cut, which is now 188rwhp. Eric is the man on the bubble, so post some numbers and bump him off already. tongue.gif I didn't include JasonsTSi because those numbers were on an engine dyno and not a chassis dyno, and they're just not comparable. smokinHawk did his on a Mustang dyno, which tends to read lower than a Dynojet, so I let that slide since it gives him no advantage. Brian, let me know if you want your cars on the list and I'll put the numbers in your sig up.
-
Yeah, Airborn was one of them that I found. This one was the other: http://www.techlinecoatings.com/Exhaust.htm Check out the Black Satin (BHK). 2000F and it can air dry.
-
My research has only been for a turbo car, but a 1600F coating would be borderline for me. The stuff I was looking at is rated to 2000F, and is a thermal barrier.
-
The best ceramic coating materials in terms of resisting heat are satin black in color. (It has nothing to do with the color, but the chemical composition) All of the coating places are generally using the same sets of chemicals, btw. I'm probably going to get some over the winter and see how it works. If I can find a link to the stuff I was looking at, I'll post it.
-
You found your answer. Typically, a RRFPR is used as a fueling device with undersized injectors to add more fuel as boost increases. A "normal" FPR simply raises pressure with boost so that net pressure remains constant. If your injectors have sufficient flow for your horsepower level, you stick with an FPR.
-
No. tongue.gif Actually, I was hoping that enough people would post #s so that I could fill out the rest of the spots. I'll probably get around do doing something with it later this afternoon.
-
Light coating of oil on brake rotors?!?! Are you NUTS?!?!?! Man, if you hate Howard then just tell him. Don't try to kill the guy. tongue.gif
-
Whenever you start putting the turbo in, I'll be happy to come over and help/watch/laugh, though. smile.gif